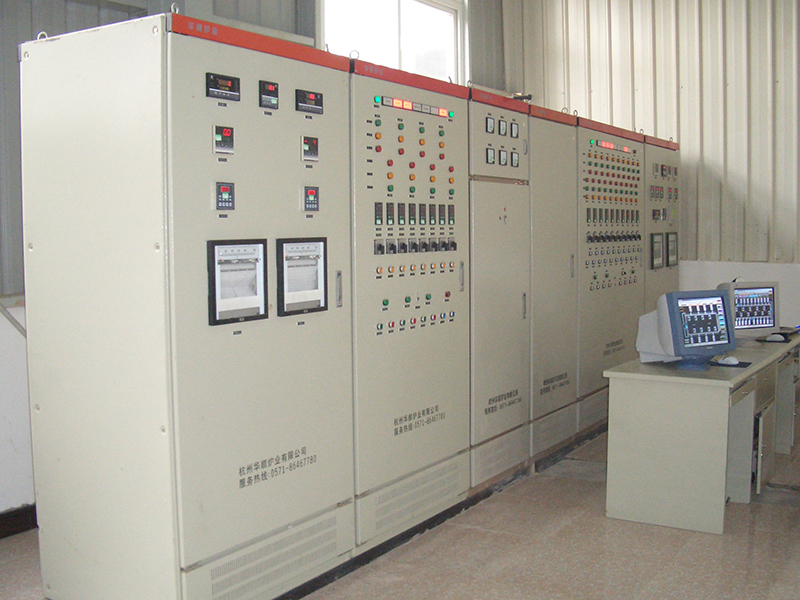
Introduction to PLC computer control:
(1) . system composition
The electric automatic control system of trolley type gas heat treatment furnace adopts hs-dcs type calculator distributed control system based on Siemens S7-300 series PLC. The upper computer adopts Advantech ipc610-p Ⅳ industrial control computer and Siemens wicc6.0 configuration software as the upper monitoring configuration software, which makes the whole monitoring system interface friendly, and realizes dynamic display of system flow chart, process curve setting, real-time monitoring, query and print historical data records.
Siemens S7-300 series PLC is adopted as the lower level. SIMATIC S7-300 is a general-purpose PLC. It is a modular controller specially designed to meet the analog and digital control requirements of medium-sized process devices. It is especially suitable for industrial furnaces, environmental protection equipment, heating devices and other similar program control, and can flexibly realize a variety of control.
The control algorithm configuration of the lower PLC is completed by PLC configuration and programming software package STEP7 based on S7-300 on an independent PC, and then downloaded to the controller as a complete file with the serial port of calculator to realize the functions of temperature control, pressure control detection and fault detection alarm.
Siemens wicc6.0 monitoring configuration software based on Windows XP operating system and S7-300 running on the upper computer can achieve seamless combination, and improve the stability and reliability of the control system.
The distributed control system of hs-dcs calculator consists of a set of Advantech IPC 610-p IV industrial control computer, 19 inch Samsung LCD imported display, communication board, optical recording, Sound Blaster, sound system, I / O board, ups and other peripheral equipment. The system has large storage capacity (frequency 2.8g, memory 2G, hard disk 160g), high speed, strong anti-interference, high reliability and strong adaptability to harsh environment.
The automatic control system adopts hs-dcs distributed control system and special German hokkod ies258 controller, and the valve parts adopt advanced components such as German hokkod company executive components and electronic electric actuators. The above combination has advanced performance and high reliability.
Due to the adoption of high reliability components and mature industrial furnace control technology, the process flow, heat treatment precision and automatic control operation level of the whole heating furnace have reached the domestic advanced level, which ensures the heat treatment quality of products and the reliability of the system.
Dynamic process flow chart
This screen will fully and dynamically display the dynamic process flow of operating heat treatment furnace. The combustion state of each high-speed burner (ignition, large and small fire, flameout) and mouse type manual automatic control. Dynamic monitoring and control of pressure system and temperature control system.
Production chart
In the form of production table, this screen dynamically displays the measured temperature, set temperature, deviation temperature, alarm limit, output proportion of temperature control meter and the status of each burner; the set value and measured value of each pressure system and the switch status of each control valve. The operator can modify the set value and alarm limit directly on the table with the mouse.
Process curve setting, recording and historical data recording:
These two screens will fully record or set the process curve. The setting of process curve is very simple and intuitive. The record of actual operation process curve is displayed in different colors and saved in real time. Historical data record will continuously record all kinds of historical data and measured process curve in the past.
Temperature control system
The heat treatment furnace is equipped with 18 temperature control thermocouples on both sides of the furnace. It forms a control PID cycle with hs-dcs distributed control system and high-speed automatic control burner. The furnace is divided into 18 temperature control areas to automatically control the temperature of each zone in the furnace and keep the temperature in the whole furnace uniform.
The furnace temperature is recorded in the operating station of hs-dcs control system, and the record and display of historical curve can be configured arbitrarily.
Pressure control system
The heat treatment furnace is equipped with gas pressure automatic control system, gas under pressure emergency cut-off and alarm control system, combustion air pressure automatic control system, furnace pressure automatic control system and alarm system.
The gas pressure system also has the function of automatically shutting off the gas source and alarming when the fan fails, so as to ensure safe production. The gas pipeline is also equipped with a flow digital display meter.
Combustion control system
The core of combustion control system is hsk-b intelligent combustion controller, which is composed of ies258 controller from Germany, ignition transformer imported from Italy, ignition / flame pick-up electrode imported from Italy, electromagnetic valve and other components. In addition, the pulse control application software specially developed is mature and reliable, and the failure rate is extremely low.
The combustion control system has two control modes of "remote" and "local". In the "remote" state, the combustion system and hs-dcs control system constitute a dead cycle automatic control system. The switch of burner and adjustment of large and small fire are controlled by hs-dcs control system. Once the system fails, it will switch to "local" operation, and the local control will be realized by the hokkod ies258 controller in the controller.
The combustion control system is equipped with automatic flame monitoring and power-off valve closing protection functions. Once the burner flameout or the combustion is not good, the control system will immediately cut off the gas valve and alarm. At the same time, all valves are of electric closing type. Once the power is cut off, the valves will be cut off automatically to prevent safety accidents.
The switch, big and small fire, flameout status and control signals of each burner are transmitted to hs-dcs control system through Siemens PLC I / O module hard circuit and monitored.
Fault detection and alarm system
The heat treatment furnace is equipped with complete fault detection, alarm, diagnosis and safety protection functions. All kinds of fault display adopts fault alarm module. There are light and audio-visual alarm on the control cabinet and voice alarm on the calculator.
Field control system
The electric control system includes power control system, wires and cables, field electrical installation, etc. The operation system of furnace door and car completes the lifting of furnace door and the entry and exit of furnace car, and the actions are interlocked with each other.
All limit switches are made of Honeywell components with double insurance. Large fan adopts Y - △ depressurization starting mode. And interlock with controller.
The thermocouple compensation wire and communication line are shielded wire to ensure reliable measurement.
Superior network system
1. Communication network structure: the industrial control computer adopts cp343 and PLC Ethernet communication module to form Ethernet, and realizes data exchange with upper L2 through 10m / 100M network card; the area is connected with twisted pair, and the partition is connected by optical fiber provided by the buyer (optical fiber coupler is provided by the user).
2. Data communication: between HMI and L2: message mode is adopted for conventional non real-time data exchange, and OPC mode is adopted for real-time data. TCP / IP protocol based on Industrial Ethernet can be used between HMI and PLC.
3. Functions achieved:
Δ can receive material, process parameters, production plan and other data from L2 for direct production;
Δ track and file the materials in the furnace area;
Δ upload production performance;
Δ set and modify the furnace process parameters in this area;
Δ real time monitoring, printing and filing of furnace thermal parameters in this area;
Δ monitor, collect, print and confirm the fault information of the furnace in this area;
Δ query the historical data of furnace;
Δ L2 can be uploaded;
(2) main characteristics of networked control system
Open: integrate various standardized software and hardware interfaces, and easily access Industrial Ethernet, third-party distributed control system and logic controller networking through DP twisted pair.
Compatibility: digital signal conforming to fieldbus standard and traditional analog signal coexist in the system. It makes the current industrial automation scheme and the implementation of fieldbus technology simple and easy.
Safety: the system safety and anti-interference meet the international standards in the industrial environment.
Integration: hs-dcs system is an open and extensible system, which can be easily expanded and integrated, so that users can add custom applications of the third party according to their special needs.
Field Intelligence: advanced equipment management function is added, parameter setting of intelligent transmitter on fieldbus is realized to realize automatic management, and the combination of equipment management and process control is achieved.
Graphic interface: provide integrated graphical interface Siemens wicc6.0 configuration tool, which can easily and quickly generate graphical interface and provide a variety of predefined library objects.
Real time simulation: the system has the function of off-line real-time debugging and simulation, which shortens the debugging cycle and reduces the risk of scheme implementation.
Remote service: remote monitoring, fault diagnosis, system maintenance, operation guidance and system upgrade can be realized through remote communication media.
Fault diagnosis: with system and transmitter or sensor fault diagnosis function, high degree of intelligence, easy to eliminate thermocouple wire break and other faults.